“Persone, Qualità e Sicurezza, Flusso, Efficienza”
Servizi Italia e le Centrali di Sterilizzazione
Il Gruppo Servizi Italia si pone come partner globale per la fornitura di servizi ai settori della sanità e dell’industria. L'attività produttiva si svolge in 56 impianti produttivi situati in Italia, Brasile, Turchia, Marocco, Albania, India e Singapore. Il gruppo offre soluzioni globali integrate in ambito sanitario, ponendosi come interlocutore unico e proponendo un’offerta ampia, altamente specializzata. I principali servizi offerti sono:
- Lavaggio e noleggio di biancheria piana (lenzuola, traverse, coperte), biancheria confezionata (camici, divise ospedaliere), materasseria e guanciali. Trattamento abiti da lavoro e abiti degli ospiti di case di cura/residenziali.
- Sterilizzazione di Tessuto Tecnico Riutilizzabile per camici operatori, kit procedurali e teli per l’attività chirurgica, oltre a parti accessorie in materiale monouso.
- Sterilizzazione Strumentario Chirurgico: ritiro, ricondizionamento, manutenzione e sterilizzazione dello strumentario chirurgico, ricomposizione kit. Gestione della Centrale di Sterilizzazione, progettazione, installazione e ristrutturazione dei siti affidati in appalto dalla Aziende Ospedaliere, validazione e controllo dei processi di sterilizzazione.
La figura rappresenta alcune foto del prodotto lavorato e di una Centrale di Sterilizzazione.
L’idea e gli obiettivi
Prendendo spunto da una difficoltà contingente in una Centrale di Sterilizzazione di un importante Ospedale in cui Servizi Italia è appena subentrata, l’azienda ha deciso di attivare un percorso KAIZEN™ non solo per risolvere la criticità, ma soprattutto per definire un proprio modello di eccellenza, come riferimento e guida per le altre Centrali, attuali e future.
Gli obiettivi del Progetto sono stati:
- Coinvolgere il personale delle Centrali e la struttura della Sede
- Assicurare un servizio di eccellenza agli Ospedali
- Migliorare la competitività per sostenere e sviluppare il business.
Il Cantiere Gemba KAIZEN™
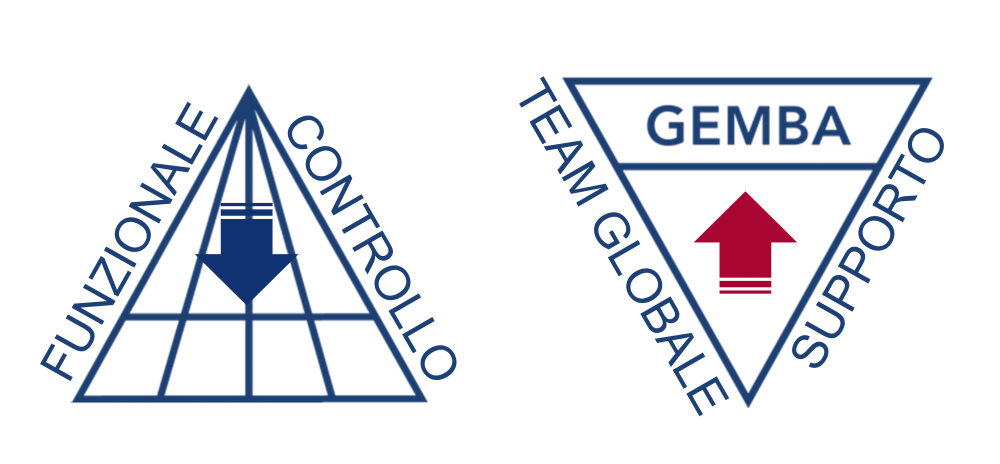
Il concetto Gemba (Gemba vuol dire posto reale, dove lavorano le persone e si crea il valore per il Cliente) rappresenta il cuore di Kaizen. Sta a significare che le soluzioni e gli standard operativi non sono definiti e calati dall’alto, ma sono sviluppati nel Gemba con il coinvolgimento e la condivisione delle persone e con il supporto da parte del management.
Il cantiere Gemba KAIZEN™ è il sistema per attivare il team e portare alla soluzione nuova.
Il Team del Cantiere
È stata scelta la Centrale di Sterilizzazione pilota e il team del Cantiere è stato costituito dalla responsabile e dal personale della Centrale e dalle funzioni di supporto della sede.
La formazione iniziale del team sui Fondamenti KAIZEN™ è stata realizzata direttamente nel Gemba della Centrale.
I tre pilastri del Modello di Eccellenza KAIZEN™
Il modello di eccellenza è stato costruito su tre pilastri:
- Qualità e Sicurezza: la qualità del servizio passa attraverso la qualità dei processi e la responsabilizzazione di tutti gli operatori, in sicurezza assoluta ed in logica poka-yoke. Senza qualità e sicurezza non si va da nessuna parte.
- Flusso: il flusso produce il servizio e lo consegna al cliente Ospedale o Centro Ambulatoriale, in logica di minimo tempo di attraversamento e di flessibilità mix free.
- Efficienza: è l’altra condizione per essere competitivi: efficienza di flusso unita ad efficienza di risorsa.
Le condizioni essenziali del modello (e di ogni altro modello in logica Kaizen) sono quelle di essere:
- Flessibile, capace di adattarsi alle diverse situazioni.
- Evolutivo, aperto agli sviluppi ed al miglioramento continuo.
Qualità e Sicurezza
Il concetto KAIZEN™ di Qualità riporta alla logica di qualità nel processo, progettato per prevenire la possibilità di errore (Poka-Yoke), ed al principio di autocontrollo degli operatori, ai quali è affidata la responsabilità di fermare il processo stesso in caso di anomalia (AutoQualità). Nel cantiere tutti i processi sono stati analizzati secondo questi principi e sono stati ridefiniti sia gli standard operativi, sia gli standard di relazione con il Cliente Ospedale (che ospita la Centrale nella sua struttura), il quale consegna il kit dei ferri chirurgici post-intervento secondo gli standard concordati con la Centrale.
Per la sicurezza, si è fatto riferimento rigoroso ai principi delle 5S in ambiente sanitario.
Flusso
Il modello KAIZEN™ FSL - Flow Synchronization Leveling ci guida nella creazione del flusso, nel sincronizzare i diversi processi/risorse (macchinari e operatori), e nel livellare capacità e carico. Il flusso viene attivato dall’arrivo del kit dall’Ospedale ed il carico dipende da numero e tipo degli interventi chirurgici eseguiti giorno per giorno.
La velocità di riconsegna dopo la sterilizzazione consente di tenere lo stock di kit pronti per l’intervento al minimo, in funzione dell’operatività dell’Ospedale.
Il principio base di questi servizi (così come di tante aziende manifatturiere al giorno d’oggi) è quello che chiamiamo mix free, capacità di essere flessibili e di adattare la capacità produttiva alla domanda, così come questa arriva in termini di volumi e mix.
Nel cantiere è stata sviluppata una soluzione innovativa per la gestione del flusso ispirata come sempre al principio guida di Taiichi Ohno e basata sull’integrazione di questi elementi:
Produzione sincronizzata. Il flusso gestisce i processi secondo il ciclo di lavoro, entrando nelle sequenze FIFO dei processi successivi. L’eventuale urgenza (siamo in un Ospedale) è gestita in modo visual. Il criterio è quello di One Kit Flow: entrano i kit dei ferri post-intervento ed escono gli stessi kit, eventualmente revisionati o ripristinati.
Syncro Kit. Le diverse tecnologie di decontaminazione e lavaggio (area rossa) dei ferri, degli altri dispositivi elettromedicali, dei containers, “rompono” il kit che viene ricomposto prima del confezionamento (area azzurra) mediante il Syncro Kit costituito da un apposito carrello. A Kit ricostituito si va ai tavoli di confezionamento specializzati per tipologia. Si prosegue con la sterilizzazione dalla quale si accede alla preparazione della consegna al reparto dell’Ospedale o al Centro Ambulatoriale (area verde).
In questo modo si è realizzato pienamente il principio di Ohno, vero e proprio cambio di paradigma organizzativo: il capoturno non deve più fare il “vigile” sul flusso, che si sincronizza da solo, ma diventa leader e problem solver del miglioramento continuo.

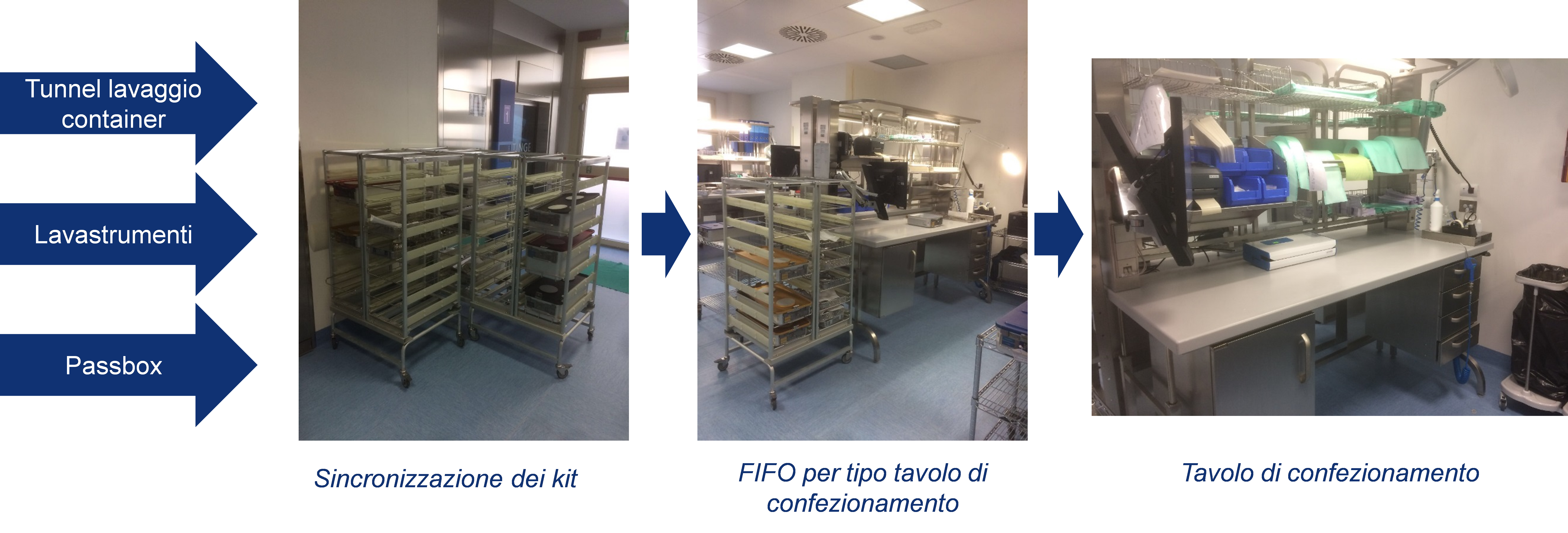
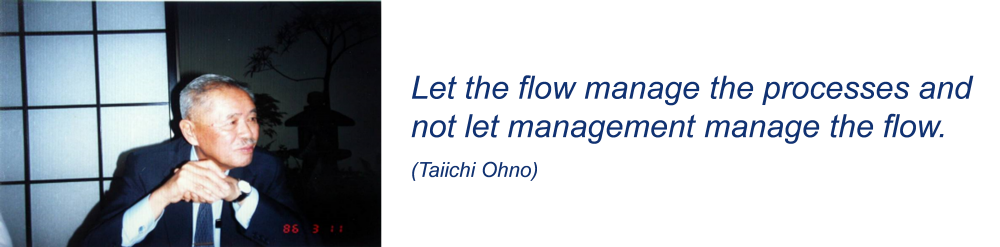
Layout. Il cantiere ha sviluppato quindi il modello di eccellenza in termini di possibili configurazioni “standard” di layout per le nuove Centrali.
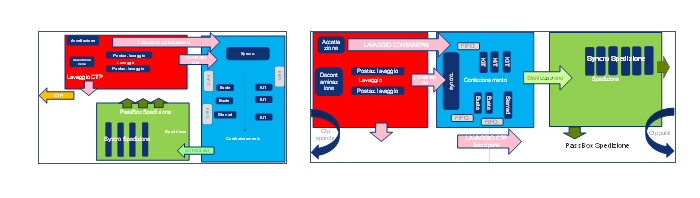
Efficienza
Il vecchio paradigma di Taylor ci insegnava a separare le risorse per poterle ottimizzare (ottimo globale ottenuto dalla somma degli ottimi locali). Questo ha portato al concetto di Efficienza di Risorsa: separazione e specializzazione delle tecnologie, delle funzioni e delle responsabilità (“siloed organization”), tecnologie ad alta velocità a scapito della flessibilità, il famoso “lotto economico”.
Il focus è sulla risorsa. Il cliente non esiste in questo paradigma.
Il nuovo paradigma KAIZEN™ cambia il punto di vista: dalla risorsa al processo globale che porta il valore al cliente: il focus è sul cliente, non più sulla risorsa. E di conseguenza sul flusso. Il nuovo concetto è l’Efficienza di Flusso.
La sfida diventa quella di raggiungere lo stato ideale di alta efficienza di flusso unita ad alta efficienza di risorsa, subordinando organizzazione e tecnologie. L’organizzazione si caratterizza nella logica One Team e nei meccanismi circolari di funzionamento (che noi chiamiamo Syncro e Daily Kaizen).
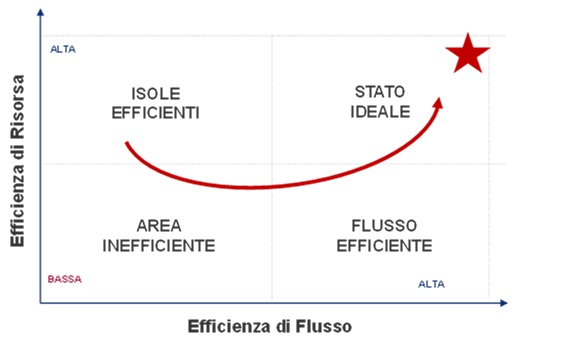
Nel cantiere della Centrale di Sterilizzazione l’efficienza di flusso ha portato ad accorciare il tempo di attraversamento e di riconsegna dei kit, realizzando un livello di servizio di eccellenza.
Gli interventi sulla flessibilità delle tecnologie e degli operatori (ad esempio sui turni di lavoro variabili in funzione della domanda e sulla polivalenza) ha portato ad aumentare la produttività globale del sistema (ore lavorate e stock dei materiali).
Il miglioramento quotidiano
Una volta migliorato il processo generale con il cantiere Gemba KAIZEN™ attraverso il team di cantiere, la nuova situazione ed i nuovi standard sono “consegnati” ai team naturali rappresentati dai responsabili e dal personale delle unità organizzative permanenti, per il controllo della performance ed il miglioramento continuo degli standard stessi (logica PDCA).
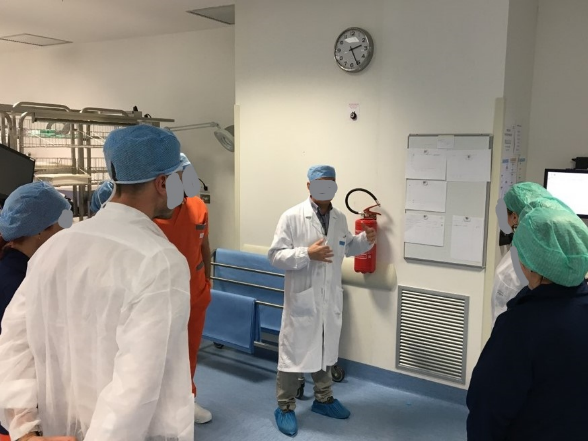
Il sistema Daily KAIZEN™ è il sistema per allenare i team naturali e costruire la cultura del miglioramento continuo, secondo il concetto One Team.
La logica TWI assicura la condivisione, il training e l’applicazione degli standard sviluppati nel cantiere.
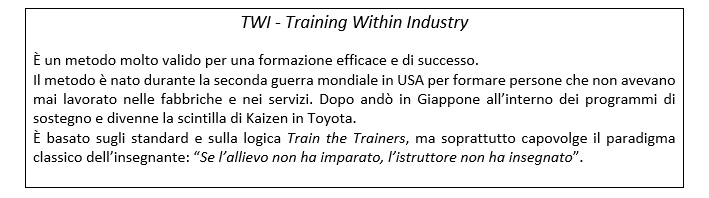
La Road Map per l’estensione del Modello
È quindi stata definita la road map per l’estensione del modello alle altri Centrali e per il training del personale. Alla responsabile della Centrale pilota (e del cantiere) è stata assegnata la responsabilità del piano di estensione e di training.
È stata inoltre coinvolta la funzione aziendale specifica per l’utilizzo del modello come leva competitiva nelle gare per nuove Centrali.
I risultati
Sono espressi dalla soddisfazione di tutto il team del cantiere e del personale delle Centrali per il forte coinvolgimento e la condivisione del lavoro fatto, e dalla crescita professionale degli operatori.
Risultati di performance
- Livello di servizio all’Ospedale e ai Centri Ambulatoriali 100%
- Qualità del processo - Riduzione forte delle non conformità (già ampiamente sotto i livelli contrattuali) -50%
- Sicurezza - Zero incidenti e “near miss”
- Flusso - Riduzione del tempo di attraversamento -25%
- Efficienza - Aumento produttività e riduzione lavoro straordinario +20% - Riduzione dello stock di materiali -25%
Il Modello KAIZEN™ di Miglioramento Continuo
Gli elementi del modello completo sono rappresentati nella figura che mostra come i risultati siano superiori e sostenibili nel lungo termine rispetto al miglioramento tradizionale:
- Leadership KAIZEN™, per definire il percorso per l’eccellenza competitiva.
- Cantieri KAIZEN™, per i miglioramenti forti in logica breakthrough.
- Daily KAIZEN™, per il miglioramento quotidiano dei team naturali e la costruzione della cultura del miglioramento continuo estesa a tutta l’organizzazione.
Riflessione finale
Michele Da Ros – Direttore Linea Sterilizzazione e Dispositivi Medici
“I primi approcci verso il KAIZEN™ sono stati guidati più che altro dalla curiosità di capire se i risultati portati a testimonianza in altre realtà potevano essere trasferiti anche nelle nostre strutture produttive. Visti i cambiamenti strutturali accaduti in ambito sanitario nazionale portati dall’applicazione della spending review, emergeva la necessità di ridurre i costi senza nel contempo svilire l’elevato livello qualitativo da sempre erogato vista la delicatezza e l’importanza del servizio offerto.
In un ambiente fortemente condizionato dalla vicinanza sanitaria, KAIZEN™ dava inizialmente l’impressione di appartenere ad un mondo industriale molto lontano dalla realtà del nostro servizio.
Questo rappresentava il principale alibi e resistenza all’applicazione del cambiamento.
Spesso però accade che se all’interno di un’organizzazione cominciamo ad usare la parola magica “miglioramento”, mettendola sullo stesso piano della quotidiana necessità di “produrre in qualità”, coinvolgendo il personale operativo, ci accorgiamo che il cambiamento si autoalimenta ed emerge quasi senza fatica.
Certamente è necessaria l’analisi guidata dei processi, la misura, l’osservazione, trovare piccole soluzioni, avere l’umiltà di ripartire o tornare indietro se qualcosa non funziona, l’importante però è cercare il supporto di tutti e nel momento in cui raggiungi dei piccoli o dei grandi miglioramenti sforzarsi nel continuare a cercarli, in poche parole, sostenere.
Il cantiere iniziale ha insegnato questo e ha fatto capire che poteva esserci un’opportunità importante nel trasferire i modelli implementati in altri siti, che tali modelli potevano essere ulteriormente sviluppati e affinati. Ha fatto capire che oltre alla necessità di consegnare ai blocchi operatori kit sterili, si doveva parlare di miglioramento.
E’ evidente che è un percorso appena iniziato, condizionato dagli alti e bassi che ad esempio le difficoltà storiche che stiamo vivendo in questo periodo stanno causando, ma proprio per questo a maggior ragione va sostenuto”.